
You can either put all your slots in a single sketch (at this point this would be an easily managed sketch), or create them in pairs and successive pockets. I mapped a sketch on top of the Array shape and added two slots, then created a Pocket. This allowed me to create a single Array, with the final shape centred on the origin. What I did different from bejant is to move the original sketch from the origin, -145mm in the X axis. All its modifying tools work on 3D objects. The Draft workbench's main purpose is to create 2D geometry (it actually predates the sketcher), but it evolved to be much more.

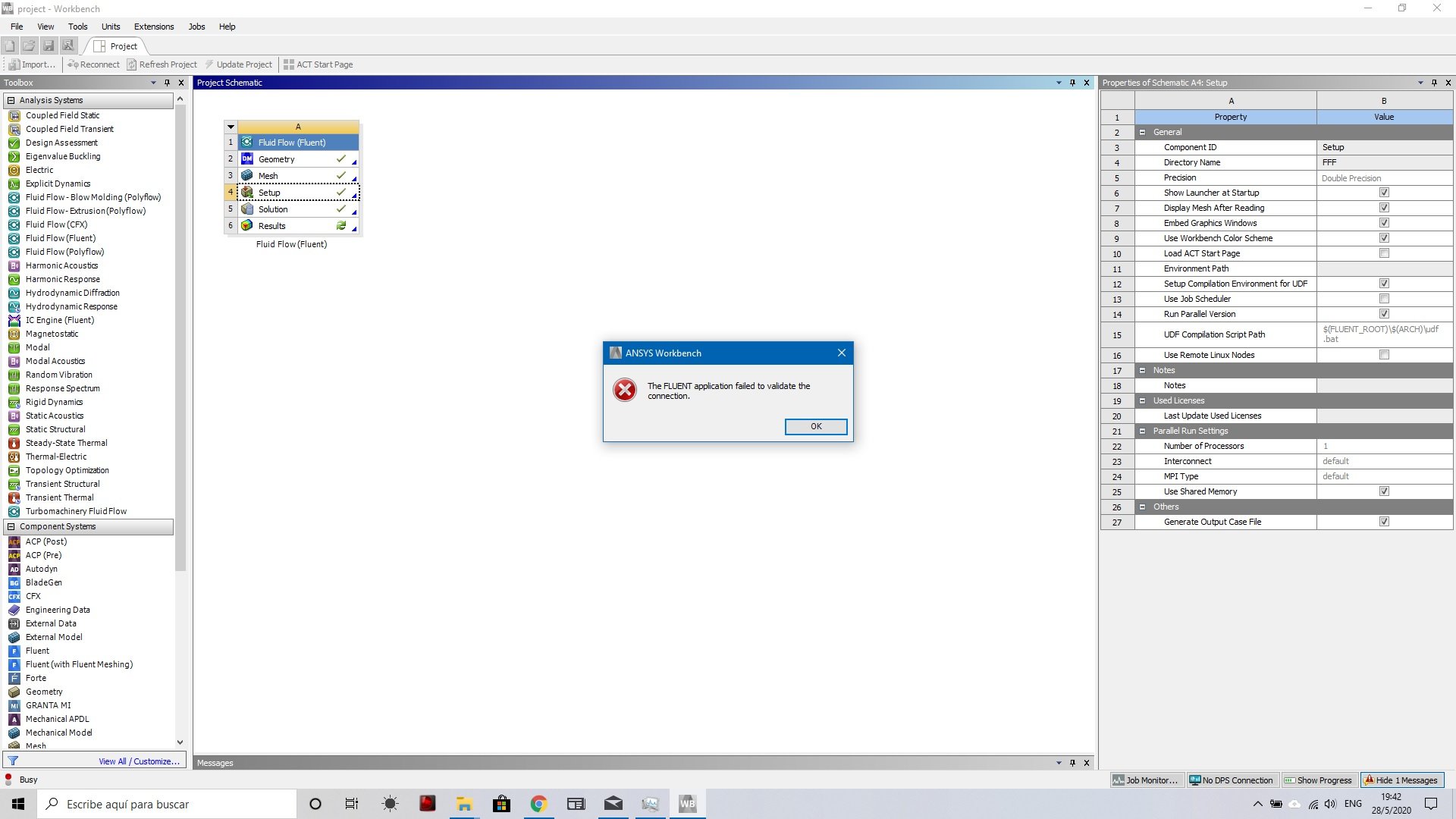
But the most efficient way that I can think of is using the Draft Array tool. You could start from a wide plate, then create successive groups of (sketch + pocket + transformation features) to get the final result. The PartDesign workbench has transformation features like linear and polar patterns, and mirrored features. Then you can add the details that didn't fit into the pattern. So it makes sense to only sketch the repetitive pattern, extrude/pad it then apply a pattern to repeat the 5 occurrences. You'll start with a solid block then you'll cut away parts of it, drill holes etc. You usually don't try to get everything in a single sketch then extrude it: you rather approach this as if you were actually going to make it from a billet of aluminium. Working in 3D is very different than working in 2D. The only way to ensure that is to connect their end points using tangent point-on-point constraints, which should replace coincident constraints. Dimensioning end points of arcs is also a bad idea because that way you can't ensure that the arcs have a perfect tangency condition with the lines they are connected to. I see you did use equal length constraints, but there are many more possible. You have many duplicate dimensions that could have been avoided using equal length constraints between elements of equal length (lines) or radius (arcs). I usually recommend to design a sketch with no more than 100 constraints, over that amount it becomes increasingly difficult to manage.Īlso, in the Sketcher you need to limit the use of dimensional constraints, they are more taxing on the sketcher solver than geometric constraints. That is one seriously complex sketch, with 243 constraints applied and 36 degrees of freedom left. Since I did spend some time writing it I'm going to post it anyway. I had basically proposed the same approach. My eyes are not as good as they were so could easily miss something. I have searched and searched and have found and fixed some breaks, but still get the error. If I am understanding this error message correctly, their is a break in the outside border of my design.
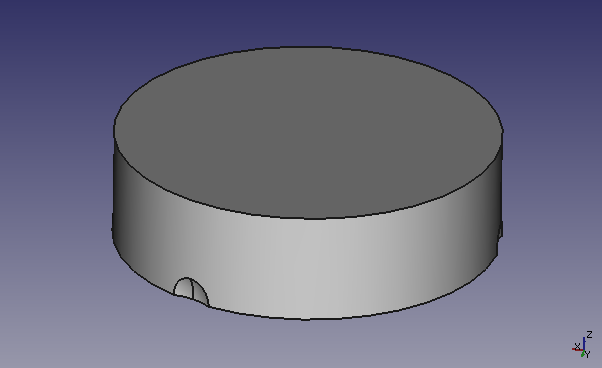
I am sure others have had this error in the past, and a search of Google did not solve the problem. I have for years hand drawn many 2D drawings. I did come first in my class for Technical Drawing in 1968. I may use the wrong words when trying to describe the my problem.
Freecad failed to validate broken face software#
I am new to this forum and new to PC software CAD design.
